Industrial blades for the automotive industry
by LUTZ BLADES
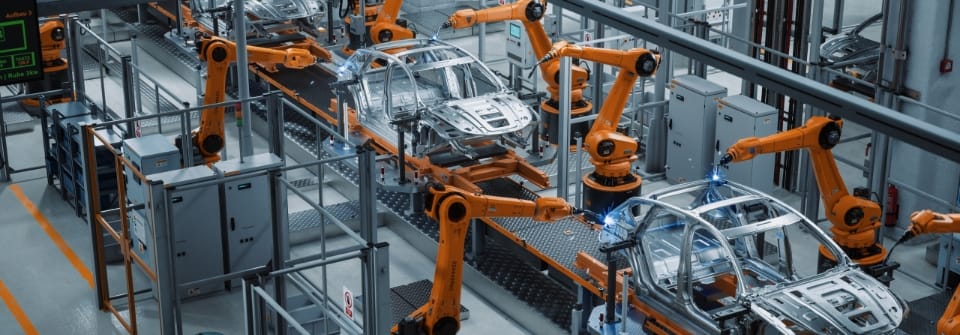
Industrial blades for the automotive industry
by LUTZ BLADES
Reliable blades
for highest quality standards
Cutting processes are of great importance in the automotive supply industry. It is particularly important that they are not only highly efficient, but also deliver high-quality results.
Whether blades for airbags, for glass processing or for deburring, whether hanger blades or special blades – as an experienced blade manufacturer for the automotive industry, we offer you the blades with which you can meet the highest quality standards.
Product recommendation
5798
Completed Projects
15
Qualified Engineers
5+
Work Facilities
3+
Worldwide Branches
The wide range of materials for our blades
Our product portfolio offers you blades in thicknesses between 0.06 – 3.0 mm and with final hardnesses between 40 – 85 HRc. You also have a wide choice in our material program:
The versatile coating program
for our blades
TiN
Standard hard material with high wear resistance and relatively high coefficient of friction (against reference material steel approx. 0.4 to 0.7), usually gold-colored, safe application range up to approx. 300 °C.
TiAlN
Has greater oxidation resistance than TiN with comparable coefficient of friction, usually anthracite blue.
Blueing / Blackening
Applied over the entire surface, light corrosion and starch protection, also serves as a distinguishing aid.
Teflon® (PTFE)
Teflon® non-stick coating (PTFE); due to the very low surface tension, practically no foreign bodies stick to the cutting edge, resistant to acids and alkalis; significantly reduced frictional resistance; the very low static friction allows jerk-free cutting (therefore very suitable for the medical sector); low wear resistance; not suitable for contact with sodium and at temperatures above 250 °C.
TiC
Has lower wear resistance than TiN with significantly lower coefficient of friction (against reference material steel approx. 0.3 to 0.5), usually anthracite colored.
ZrN
With a wear resistance similar to TiN, but denser structure (morphology) than TiN and thus greater resistance to pitting under appropriate load, usually steel colored.
CrN
Has lower wear resistance than TiN. Advantage of CrN: lower residual stresses than TiN. Therefore partially useful for applications with high bending load.
TiCN
Intermediate coating material between the high wear resistance of TiN and the low coefficient of friction of TiC, relative position between TiN and TiC depending on the ratio of C and N, usually anthracite color.
DLC
Has high wear resistance with low coefficient of friction (approx. 0.1 against reference material steel); susceptible to impact loads and high temperatures (between 100 and 300 °C depending on structure).
Color varnish
Applied over the entire surface, serves as a sorting aid for different material thicknesses and as corrosion protection.
Customized quality
Do you have individual wishes?
Do you have a question? A concern? Or a suggestion? Do not hesitate to contact us. We have the right experts for all matters, who can help you with certainty.
How can we help you?
We are pleased if we can be of further assistance to you