Sliding and hard coating
Essential For The Quality
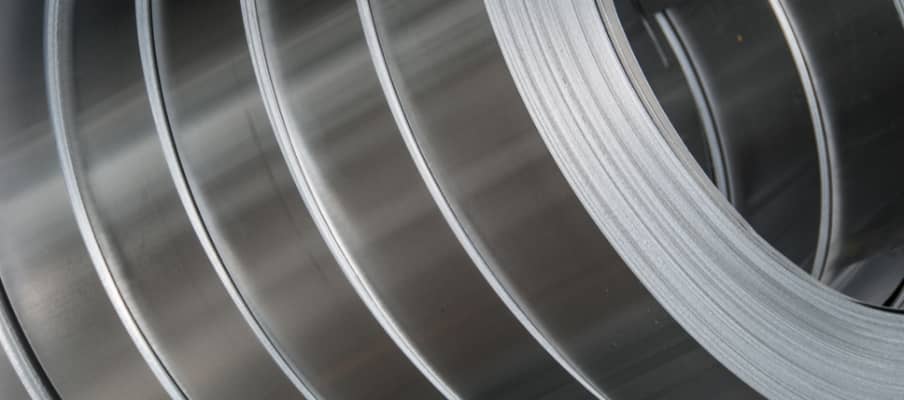
Sliding and hard coating
Essential For The Quality
High performance coatings
from Lutz Blades
How does a Coating?
Friction occurs between the blade and the material being cut. This friction leads to minute (unavoidable) damage to the cutting edge. Over time, these micro-damages “add up” and result in dulling of the cutting edge.
Solution A: Choice of a material whose nature slows down the formation of the damage.
Solution B: Choice of a coating that lies as a thin film between the cutting edge and the material to be cut.
See for yourself the performance advantages of a coated blade compared to an uncoated one here.
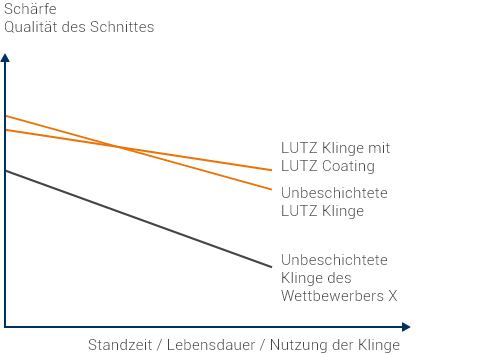
Exemplary illustration: cutting manmade fiber
The different variants of our coating program
The LUTZ BLADES coating program includes the following variants:
TiN
Standard hard material with high wear resistance and relatively high coefficient of friction (against reference material steel approx. 0.4 to 0.7), usually gold-colored, safe application range up to approx. 300 °C.
TiAlN
Has greater oxidation resistance than TiN with comparable coefficient of friction, usually anthracite blue.
Blueing / Blackening
Applied over the entire surface, light corrosion and starch protection, also serves as a distinguishing aid.
Teflon® (PTFE)
Teflon® non-stick coating (PTFE); due to the very low surface tension, practically no foreign bodies stick to the cutting edge, resistant to acids and alkalis; significantly reduced frictional resistance; the very low static friction allows jerk-free cutting (therefore very suitable for the medical sector); low wear resistance; not suitable for contact with sodium and at temperatures above 250 °C.
TiC
Has lower wear resistance than TiN with significantly lower coefficient of friction (against reference material steel approx. 0.3 to 0.5), usually anthracite colored.
ZrN
With a wear resistance similar to TiN, but denser structure (morphology) than TiN and thus greater resistance to pitting under appropriate load, usually steel colored.
CrN
Has lower wear resistance than TiN. Advantage of CrN: lower residual stresses than TiN. Therefore partially useful for applications with high bending load.
TiCN
Intermediate coating material between the high wear resistance of TiN and the low coefficient of friction of TiC, relative position between TiN and TiC depending on the ratio of C and N, usually anthracite color.
DLC
Has high wear resistance with low coefficient of friction (approx. 0.1 against reference material steel); susceptible to impact loads and high temperatures (between 100 and 300 °C depending on structure).
Color varnish
Applied over the entire surface, serves as a sorting aid for different material thicknesses and as corrosion protection.
THINGS TO KNOW
around LUTZ BLADES
around LUTZ BLADES
Of course, coatings of the cutting edge can be combined with full-surface coatings.
For every cutting task
the right blade
No matter what cutting task lies ahead of you – at LUTZ BLADES you will find exactly the right blade. Perhaps already in our rich standard range of more than 1500 blades. Or we will work with you to develop exactly the blade that is, quite literally, tailored to your specific cutting task. Our many years of experience in blade manufacturing and the availability of all necessary manufacturing steps in-house qualify us as a competent development and production partner.
Do you have individual wishes?
Do you have a question? A concern? Or a suggestion? Do not hesitate to contact us. We have the right experts for all matters, who can help you with certainty.
How can we help you?
We are pleased if we can be of further assistance to you